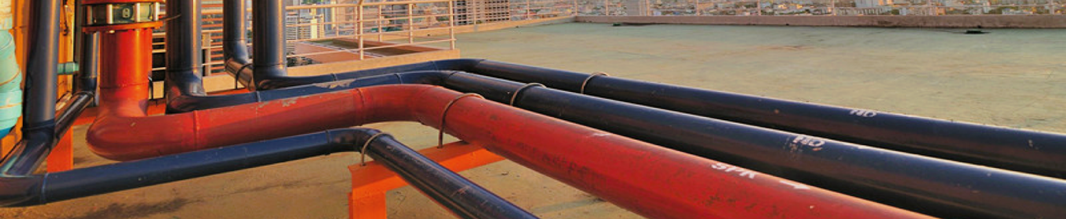
In China, city gas is extensively utilized in industrial and trade enterprises. However, the properties of hazardous gas chemicals dictate the potential for explosion risks in their utilization. Components such as pressure regulating cabinets (boxes), valve assemblies, instruments, safety valves, and burners within gas applications entail significant safety risks. In recent years, inadequate risk prevention and control measures concerning gas applications have resulted in numerous gas explosion accidents.
From 2019 to 2023, China has witnessed a noticeable upward trend in gas safety incidents. Not only has the frequency of accidents escalated annually, but their severity has also increased. Contributing factors include the aging infrastructure and subpar management of gas facilities, along with improper user practices during gas utilization. I've included below a comprehensive overview and analysis of gas safety incidents in China during this timeframe.
To systematically enhance the gas safety ecosystem, it is imperative to analyze and address the systemic causes of safety hazards in industrial and trade enterprises. Proposing corresponding preventive measures is crucial to minimize hidden hazards, mitigate risk levels, reduce potential safety threats, minimize accident losses, and ensure safe production.
Potential Safety Hazards of City Gas in Industrial and Trade Enterprises
In the inspection of 56 industrial and trade enterprises in Tianjin Binhai New Area, Jinhai District, Jinnan District, etc., our team found various problems related to gas design specifications, technical specifications, engineering construction specifications, and safety hazards. Most enterprises exhibited issues in at least one of these areas, indicating potential safety risks in the utilization of city gas within industrial and trade settings.
Table 1. Summary of Hidden Dangers Identified During Special Gas Inspections of 56 Enterprises in Tianjin
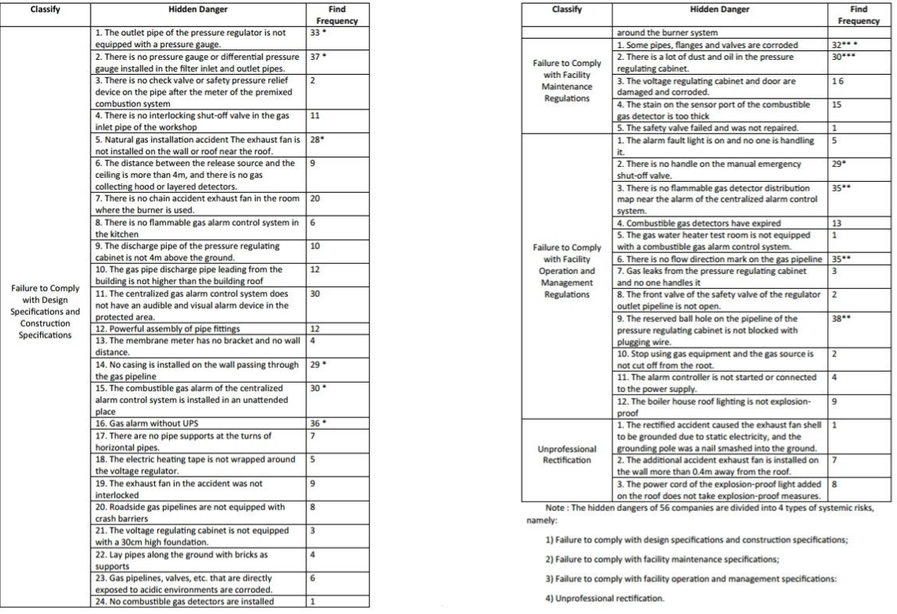
Analysis of The Root Causes of Hidden Dangers and Risk Classification in Gas Applications in Industrial and Trade Enterprises
Systemic hidden dangers and risk levels that arise during design and construction.
24 systemic hidden dangers occurred during design and construction, accounting for 55% of the total hidden dangers. 24 hidden dangers were detected 282 times, accounting for 50% of the total frequency of hidden dangers. Among the 24 hidden dangers, the detection frequency of 7 hidden dangers exceeds 50% of the sample size (56), see the items with "*" in the table. Due to the frequent occurrence of hidden dangers, systemic hidden dangers in design and construction acceptance have become the hardest hit areas. The design plan is missing items, the construction is not carried out according to the drawings, the acceptance inspection is not carried out according to regulations, and the safety risk barrier is moved to the front end of the "Turnkey project" of the gas project. There are already a lot of hidden dangers in the new project before it is used, and the existing safety risks are very high.
Systemic hidden dangers and risk levels that arise in facility operation and management.
12 systemic hidden dangers occurred during facility operation, accounting for 27% of the total hidden dangers. The 12 hidden dangers occurred 176 times, accounting for 31% of the total hidden dangers detected. Among the 12 hidden dangers, the occurrence frequency of 4 hidden dangers exceeds 50% of the sample size, as shown in the table with " ** ". The poor professional quality, non-standard operation and lack of safety awareness of operators in the use of gas are the direct reasons for many systemic hidden dangers in the operation of facilities. In the face of flammable and explosive gas, workers ignore the existing hidden dangers, and the existing safety risks are high. In addition, due to insufficient professional quality, the inspectors failed to point out hidden dangers to reduce safety risks, resulting in long-term systemic hidden dangers in the operation of the facility and high safety risks.
Systemic hazards and risk levels that arise during facility maintenance.
5 systemic hidden dangers occurred during maintenance, accounting for 11% of the total hidden dangers. The five hidden dangers occurred 94 times. Accounting for 16% of the total number of hidden dangers detected. The occurrence frequency of 2 of the 5 hidden dangers exceeds 50% of the sample size, as shown in the table with " ****”. The causes of systemic hidden dangers during maintenance are manifested in two aspects. The first is the maintenance problem of the voltage regulating cabinet. Some enterprises entrusted gas companies with maintenance. During the investigation, it was found that the facilities in the pressure regulating cabinet were rusty and the dust had not been cleaned, indicating that the gas company did not perform its duties and maintain maintenance by regulations. Enterprises that did not entrust gas companies with maintenance personnel lacked professional knowledge and had long-term problems. Without maintenance, the security risks are high. The second is the maintenance of pipelines and facilities outside the pressure regulating cabinet. The company personnel lack professional knowledge and do not know how to maintain the equipment, so they do not maintain the equipment for a long time. The lack of maintenance of urban gas facilities is one of the main reasons for production safety accidents, and the existing safety risks are high.
Systemic hidden hazards and risk levels that cannot be rectified legally.
3 systemic hidden dangers cannot be rectified illegally, accounting for 7% of the total hidden dangers. The three hidden dangers occurred 16 times, accounting for 2% of the total hidden dangers detected. Although the company actively rectified the hidden dangers pointed out by safety experts, it did not entrust a professional team to carry out the rectification. In addition to being ineffective, the rectification results may also lead to new safety hazards. The frequency of such hidden dangers is low and the existing security risks are low.
Risk Management and Hidden Danger Prevention Strategies in Gas Applications in Industrial and Trade Enterprises
To ensure the safe production of urban gas industry user enterprises and protect people's lives, property safety and public safety, the following countermeasures are proposed for risk management, control and prevention of factors causing the above four types of systemic hidden dangers.
Conduct safety assessments on urban gas industrial user project design plans and construction plans.
The state has corresponding laws, regulations, policies, and industry standards for the supervision of project design, construction, and acceptance. But no matter how good the laws, regulations, policies, and standards are, they must be implemented and supervised by someone. To control risks before potential hazards are investigated and eliminate irregularities in the "Turnkey projects" provided by the gas company to users, it is recommended to conduct a safety assessment on the project design plan and construction plan: third-party safety experts should be introduced among the project acceptance members. Achieve zero risk before "Turnkey”.
Conduct safety diagnostics on the facilities of current industrial users of city gas.
From the analysis data of 56 samples, it can be seen that there are many hidden dangers in the gas systems of enterprises currently in use, which rely on enterprise self-examination and management and special inspection and rectification over a long period. It is difficult to eradicate long-term and short-term hidden dangers. To detect and manage hidden dangers as soon as possible, hidden danger management must be carried out before the accident. It is recommended to conduct safety diagnosis on the gas facilities currently used by customers to reduce the incidence of accidents and reduce accident hazards.
Provide professional training to enterprise gas facility management personnel and hold certificates before taking up their posts.
The gas system requires personnel with professional knowledge to operate, maintain and manage everything from household pipes, pressure regulating cabinets (boxes), valve groups, instruments, safety valves, discharge pipes to burners, etc. However, the professional quality of personnel in industrial and trade enterprises is unsatisfactory. In line with the principle that professional work should be performed by professionals, given the current situation of insufficient professionalism of gas operation management personnel in industrial and trade enterprises, it is recommended that professional training be implemented for enterprise gas facility managers and that they must hold certificates to work. Establish an expert database for special gas inspections. Special inspections of gas in industrial and trade enterprises should be carried out at least once a year. However, some hidden dangers at the site have not been discovered for a long time, which is closely related to the lack of professionalism of the inspectors. To improve the quality of gas safety inspections, it is recommended that relevant agencies establish a gas expert database, and experts will be drawn from the database for special gas safety inspections.
Implement professional design and installation of combustible gas alarm control systems.
The design and installation of combustible gas alarm control systems require specialized technical expertise and adherence to safety protocols. In instances where users lack the necessary proficiency, self-correction becomes impractical. To address potential inefficiencies stemming from in-house installations, the emergency management department should mandate that enterprises report the design and installation details of their gas alarm control systems by the "Technical Regulations for Urban Gas Alarm Control System." Only after confirmation of compliance should enterprises proceed with rectification efforts to ensure the system's effectiveness.
In summary, the comprehensive strategy to ensure the safe utilization of gas in industrial and trade enterprises should commence with intrinsic safety design processes, followed by compliant engineering construction and project acceptance procedures. Furthermore, emphasis should be placed on the safe operation of facilities and regular maintenance practices in adherence to regulations. By fostering collaboration among emergency management departments, professional institutions, and enterprises, a dual prevention system can be established to collectively mitigate hidden dangers, reduce risk levels, minimize potential losses from production safety accidents, and uphold safe production standards.